Understanding and Utilizing FRP Rectangular Tubes A Comprehensive Overview
Fiberglass Reinforced Plastic (FRP) rectangular tubes, also known as GRP (Glass Reinforced Plastic) tubes, have gained significant recognition in various industries due to their exceptional properties and versatility. These tubes are constructed by combining a thermosetting resin matrix with glass fibers, resulting in a composite material that offers an ideal balance of strength, durability, and lightweight.
The rectangular shape of FRP tubes provides several advantages over traditional round pipes. Primarily, they optimize space utilization, making them particularly suitable for applications where width is more critical than depth. For instance, in structural support systems, HVAC ducting, or electrical conduit systems, the rectangular design allows for better alignment and fitting within confined spaces.
One of the key features that set FRP rectangular tubes apart is their corrosion resistance. Unlike metal pipes, they do not corrode when exposed to harsh chemicals, acidic or alkaline environments, or extreme weather conditions. This makes them ideal for use in chemical processing plants, offshore platforms, and wastewater treatment facilities.
In addition to their chemical resistance, FRP rectangular tubes exhibit high strength-to-weight ratio. They can withstand heavy loads and impacts without deforming, making them suitable for load-bearing structures. Furthermore, they have excellent electrical insulation properties, rendering them perfect for electrical installations and grounding systems.
The manufacturing process of FRP rectangular tubes involves pultrusion, a technique that impregnates continuous glass fiber rovings with resin and then pulls them through a heated mold to form the desired shape
The manufacturing process of FRP rectangular tubes involves pultrusion, a technique that impregnates continuous glass fiber rovings with resin and then pulls them through a heated mold to form the desired shape
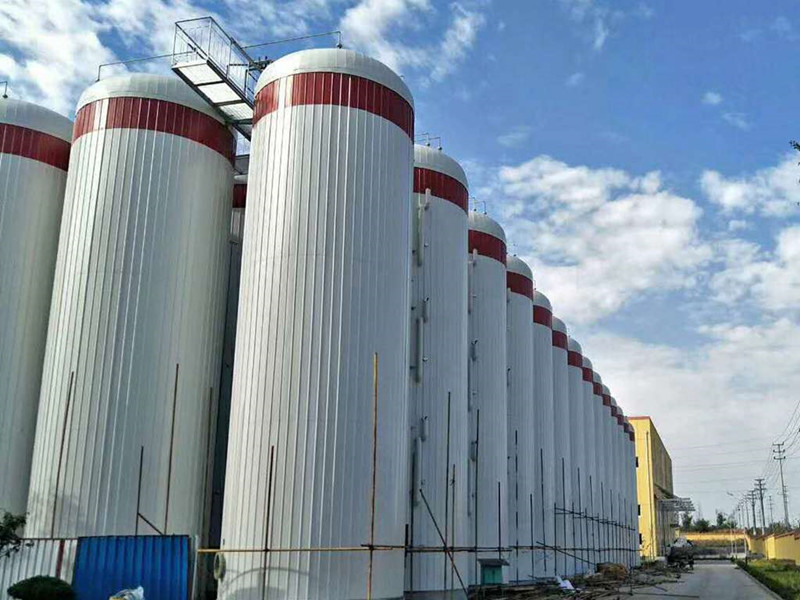
The manufacturing process of FRP rectangular tubes involves pultrusion, a technique that impregnates continuous glass fiber rovings with resin and then pulls them through a heated mold to form the desired shape
The manufacturing process of FRP rectangular tubes involves pultrusion, a technique that impregnates continuous glass fiber rovings with resin and then pulls them through a heated mold to form the desired shape
frp rectangular tube. This process ensures consistent quality, precise dimensions, and the ability to produce tubes in lengths up to several meters.
Another advantage of FRP rectangular tubes is their ease of installation and maintenance. They can be easily cut, drilled, or joined using various methods like mechanical fittings, bonding agents, or welding, without compromising their integrity. Their non-conductive nature also reduces the risk of electric shocks during installation or maintenance.
Despite these benefits, it's essential to note that like any material, FRP rectangular tubes have limitations too. They may not be suitable for high-temperature applications or situations requiring high-impact resistance beyond their designed specifications. However, with proper selection and engineering, these drawbacks can be mitigated.
In conclusion, FRP rectangular tubes are a game-changer in the world of construction and engineering. Their unique combination of strength, durability, corrosion resistance, and lightweight makes them a preferred choice for numerous applications. As technology advances, it's expected that the usage and efficiency of FRP rectangular tubes will continue to grow, revolutionizing the way we build and innovate.