In the ever-evolving landscape of construction and industrial applications, FRP (Fiber Reinforced Polymer) dampers have emerged as game-changers, providing innovative solutions for vibration control and structural stability. As industries continue to demand high-performance materials that are both cost-effective and sustainable, the role of FRP dampers has taken center stage due to their unique properties and advantages.
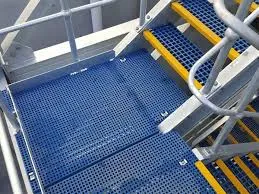
Experience in the field demonstrates that FRP dampers significantly surpass traditional damping systems in terms of durability and resistance to harsh environments. Users in industries such as civil engineering and architecture have reported remarkable improvements in the longevity and reliability of their structures. The integration of FRP dampers into building designs helps mitigate issues related to vibrations from natural events like earthquakes and strong winds, enhancing overall structural integrity. Case studies from around the globe confirm that structures incorporating FRP dampers experience less fatigue and lower maintenance costs over time, attesting to their long-term value.
From an expertise standpoint, FRP dampers are crafted from composites that blend advanced resin systems with high-strength fibers like glass, carbon, or aramid. This composition grants them unparalleled flexibility and strength-to-weight ratios, outshining traditional metal-based damping systems. Engineers appreciate this versatility, as it enables custom-tailored solutions specific to each project's requirements. By adopting FRP technology, structures are able to achieve higher efficiency with less material, making them an ideal choice for projects with weight constraints or for applications requiring transportability.
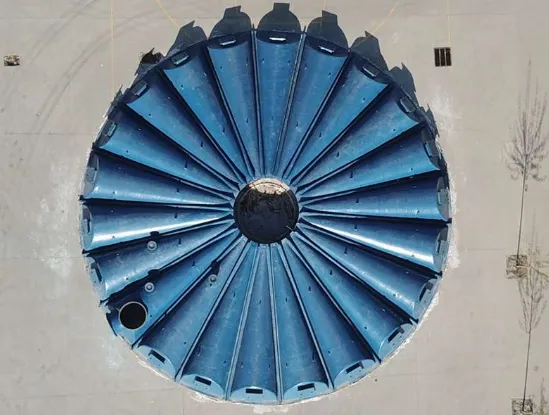
Further amplifying their authority in the field, research studies conducted by leading universities and independent laboratories underscore the performance of FRP dampers in a variety of conditions. Extensive testing evidences their superiority in temperature resilience and chemical stability, making them suitable for use in extreme environments where traditional dampers would falter. Published research highlights how FRP dampers effectively absorb and dissipate vibrational energy, proving essential in protecting both infrastructure and sensitive equipment housed within.
frp damper
Trustworthiness of FRP dampers is bolstered by rigorous industry standards and certifications they consistently meet or exceed. Compliance with standards such as ISO, ASTM, and others ensures that FRP dampers are reliable, safe, and efficacious. Manufacturers of FRP dampers frequently provide detailed documentation and transparent testing results, enabling engineers and procurement specialists to make informed decisions. Testimonials from satisfied clients across sectors—from transport to renewable energy—corroborate the dependability and effectiveness of these damping solutions.
Expert opinions also emphasize the eco-friendly nature of FRP dampers as a noteworthy advantage. Traditional dampers, often made of metals that are susceptible to corrosion, not only require frequent replacement but also contribute significantly to environmental waste. In contrast, FRP dampers offer enhanced corrosion resistance, reducing the ecological footprint by prolonging the lifespan of damping systems and minimizing the need for periodic maintenance. Moreover, the production of FRP dampers leverages less energy-intensive processes, further aligning with sustainable construction practices.
The evolution of FRP dampers demonstrates an ongoing commitment to innovate within the industry, illustrating how modern materials can elevate the standards of construction quality and efficiency. As more industries realize the myriad benefits associated with fiber-reinforced polymers, their adoption is expected to rise, paving the way for smarter, more resilient structures worldwide. The narrative of FRP dampers is one of triumph through technical advancement, setting the stage for future discoveries that continue to redefine what is possible in structural engineering and vibration damping applications.