Fiber Reinforced Plastic (FRP) fittings represent a significant advancement in the world of industrial piping systems. These innovative solutions cater to a diverse range of industries, including chemical processing, wastewater management, and even offshore drilling. The escalating demand for durable, corrosion-resistant materials makes FRP fittings an ideal choice for enterprises seeking efficiency and longevity in their operations.
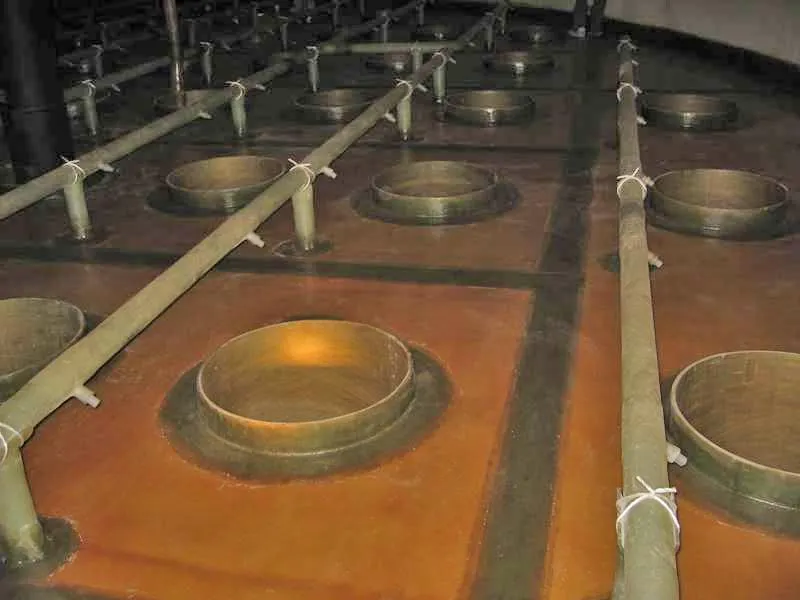
FRP fittings are renowned for their unparalleled resistance to corrosive chemicals and environmental stressors. Unlike traditional materials such as steel or iron, FRP does not succumb easily to rust or chemical degradation. This inherent resilience makes it particularly advantageous for industries dealing with aggressive chemicals or extreme weather conditions. As a result, companies can significantly cut down on maintenance costs and downtime caused by material failure.
An important aspect of FRP fittings is their lightweight nature combined with strength. This unique feature simplifies the installation process, often requiring less labor and time compared to heavier metal counterparts. Companies have reported substantial reductions in installation time, directly translating to cost savings and swift project completion. Additionally, the lightweight property of FRP reduces the load on supporting structures, enhancing overall system stability and reducing the risk of infrastructure stress over time.
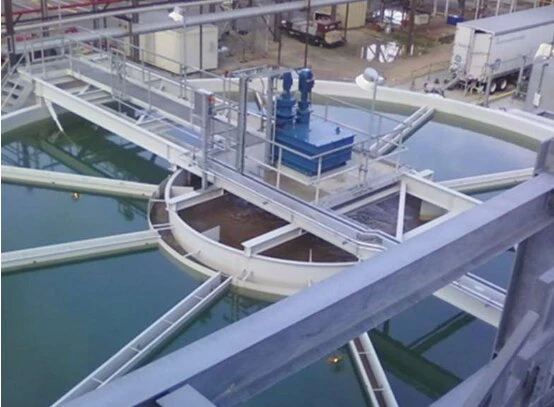
The engineering behind FRP fittings ensures flexibility and customization. Manufacturers can tailor the fittings to precise specifications, accommodating unique installation requirements or complex system designs. This flexibility is particularly beneficial in retrofitting projects where existing structures may not have standard measurements. Customizable FRP solutions thus offer adaptability that is hard to achieve with more rigid materials.
frp fittings
Furthermore, the environmental benefits of FRP fittings cannot be overstated. As sustainability becomes a central concern in industrial operations, using FRP aligns with green initiatives due to its long lifecycle and minimal environmental footprint. When considering full lifecycle cost assessments, FRP often emerges as a more economical choice—not just in terms of initial purchase, but through reduced energy consumption during manufacturing and lower emissions during the product lifespan.
The trustworthiness of FRP products is backed by extensive research and field testing. Reputable industry standards and certifications ensure that FRP fittings consistently meet rigorous quality benchmarks. This authoritative foundation provides decision-makers with confidence that their investments in FRP solutions are sound and reliable.
Purchasing FRP fittings from credible suppliers further enhances this trust. Established suppliers offer not just products but also expert guidance and support throughout the lifecycle of the fittings. This partnership approach reassures businesses that they have invested in a solution that will support their operational goals over the long term.
In conclusion, FRP fittings are not just an alternative to traditional materials; they represent a forward-thinking approach to industrial design and maintenance. With their ability to withstand harsh environments, ease of installation, and environmental benefits, FRP fittings are a critical component for industries looking to optimize performance and sustainability. By choosing FRP, businesses align themselves with future-ready solutions that promise a robust return on investment and operational peace of mind.