Choosing the right mandrel can significantly impact the efficiency and quality of your manufacturing processes. Mandrels are essential tools in various industries, including metalworking, woodworking, composites, and more. Their primary function is to act as a stable core upon which materials can be shaped, machined, or processed. Understanding the nuances of mandrel application can enhance both product performance and operational productivity.
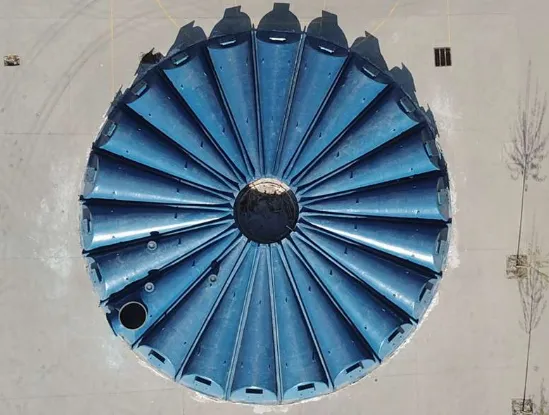
Mandrels come in numerous forms, each designed for specific tasks. The most common types include expanding mandrels, which use mechanical expansion to grip the interior of a hollow workpiece; fixed mandrels, where the workpiece is placed over a precision rod or pin; and collapsible mandrels, which are ideal for internal processing and can be easily removed after use. Each type offers distinct advantages depending on the material and process requirement.
In industries like aerospace and automotive, where precision is crucial, the selection of mandrels affects the structural integrity and functional performance of the final product. For instance, with composite materials, mandrels need to withstand high temperatures and pressures while maintaining precise tolerances. Here, a mandrel made from advanced materials such as silicone-wrapped steel cores or hydraulic inflatable designs can provide superior results by ensuring uniform pressure and reducing the likelihood of defects.
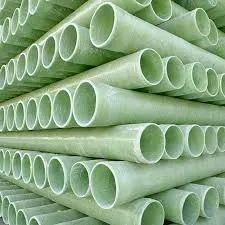
A practical experience crafting high-performance bicycle frames highlights the importance of the right mandrel. For carbon fiber bikes, the mandrel ensures the layers are accurately placed and cured, preventing weak spots. Using a thermally stable mandrel enhances the symmetry and consistency of the frame, crucial for bikes designed for high-speed performance. This example underscores the importance of aligning mandrel choice with the specific demands of the application.
Moreover, mandrel design affects not only the quality but also the cost-efficiency of production processes. A well-suited mandrel minimizes waste and reduces cycle times. For metal tube forming, utilizing a lubricated mandrel can reduce friction, which not only reduces wear and tear on the equipment but also improves the surface finish of the tubes. This dual advantage emphasizes mandrel design's role in operational efficiency.
mandrel
Authoritative industry guidance suggests consulting with mandrel manufacturers when selecting a mandrel for a new application. Their expertise can help tailor a mandrel solution that matches the precise material specifications and process conditions. With advances in technology, custom mandrels engineered with CAD systems allow for intricate designs that cater to unique manufacturing challenges, ensuring a perfect fit for complex project requirements.
Companies known for reliable mandrel production often back their products with extensive testing and validation to prove performance under anticipated conditions. Trustworthy suppliers offer certifications and test data, providing peace of mind that the mandrel will perform as expected.
Leveraging expert advice can prevent costly errors and ensure that the mandrel enhances product quality. From construction to final testing, integrating the right mandrel within the production process underpins the creation of top-tier products. Therefore, investing time in selecting an appropriate mandrel reaps sustainable long-term benefits, markedly improving quality control and reducing production costs.
In summary, the nuances of mandrel selection and application cannot be overstated. Whether your focus is on improving product durability, optimizing production efficiency, or achieving precise tolerances, understanding the diverse capabilities of different mandrels and aligning them with your business needs transforms manufacturing goals into achievable realities.