In the intricate world of industrial manufacturing and design, the mandrel holds an esteemed position for its multifaceted utility and unwavering reliability. A quintessential tool applicable in processes ranging from metalworking to the crafting of composite materials, the mandrel is more than just a support system; it’s a catalyst for precision and efficiency.
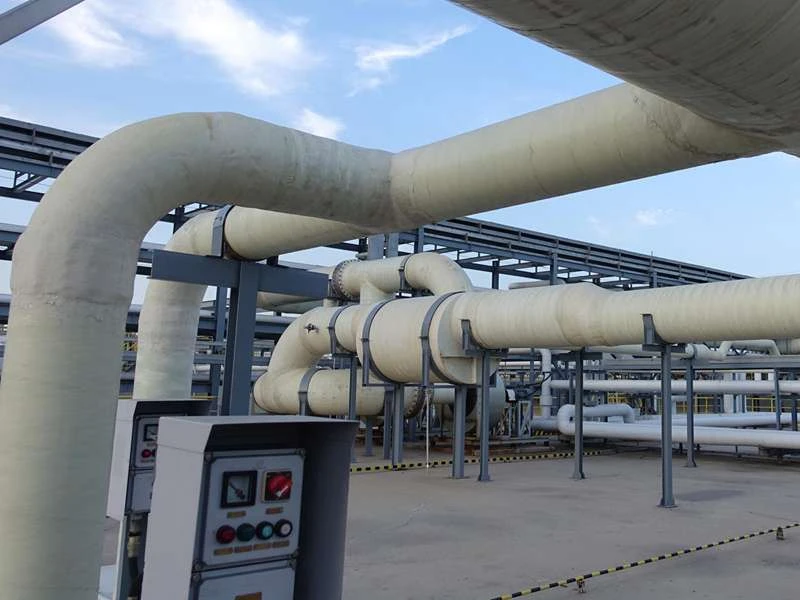
The mandrel serves as an internal support that allows for the manufacturing of hollow structures or the bending of materials without compromising their integrity. Its applications span various industries such as automotive, aerospace, and even the production of delicate medical devices. In metal fabrication, a mandrel is used inside tubes and pipes to prevent wrinkling or collapsing during processes like bending or twisting, ensuring that the final product maintains a perfect silhouette and strength.
Expertise in selecting the right mandrel can significantly enhance production quality. Materials used for creating mandrels include hardened steel, rubber, and even more advanced composites, each chosen based on the specific requirements of the task. For instance, in high-temperature environments, a metal mandrel with superior heat resistance might be employed, whereas in scenarios demanding softness and flexibility, a rubber mandrel is ideal.
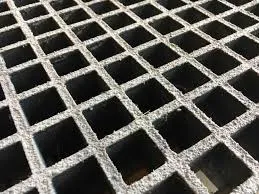
One of the most captivating examples of mandrel use is in the creation of aerospace components. The unimaginable stresses aerospace materials undergo require precision tooling where even the slightest miscalculation can lead to catastrophic failure. Mandrels made from titanium or specialized alloys cater to this need for perfection, ensuring that every inch of pipe or duct meets exacting standards.
Turning to trustworthiness and reliability, manufacturers and craftsmen across the globe rely on mandrels for consistent results. Their authority lies in the capacity to act as the unseen backbone in manufacturing, working tirelessly to support everything from custom exhaust systems to the intricate railings of a skyscraper. The trust placed in mandrels is a testimony to centuries of engineering refinement.
mandrel
In terms of experience, operators must be adept in understanding the nuances of mandrel use.
Incorrect setup may lead to product defects and inefficiencies, eroding trust in the final product. A comprehensive knowledge of how to install mandrels correctly, adjust them during processes, and recognize signs of wear can be a critical factor in maintaining operational excellence.
In modern manufacturing landscapes, the mandrel is an indispensable asset. Its role in perfecting processes, ensuring component integrity, and delivering precise, repeatable results positions it as a cornerstone of industrial efficiency. This tool is emblematic of the blend between timeless engineering principles and cutting-edge innovation. As industries continue to advance, the mandrel will undoubtedly evolve in form and material, but its foundational role will remain untouched—underscoring the astounding feat of human ingenuity in mechanical design and function.
Manufacturers seeking to optimize production lines benefit greatly by integrating mandrels into their processes. Their use not only increases output accuracy but also reduces long-term repair and maintenance costs by safeguarding against common structural anomalies. Engineers striving for excellence acknowledge that entrusting production to tools of such precision is not merely a choice but a requisite.
The evolution of mandrel design continues, with the development of smart materials and advanced computing, holding the promise for even greater innovations. As it stands today, the mandrel remains a testament to human innovation, an exemplar of engineering expertise, and an enduring symbol of reliability and trust in the industrial world.