Navigating the world of drilling equipment requires an intricate understanding of various tooling options available to enhance drilling productivity and efficiency. One pivotal element in this arena is the button tooth bit, often compared to its notable counterpart,
the toothed button bit. Both these tools hold significant value in mining, construction, and other critical drilling applications. Recognizing the nuanced differences and inherent advantages of these tools can substantially elevate your project outcomes and drilling strategy.
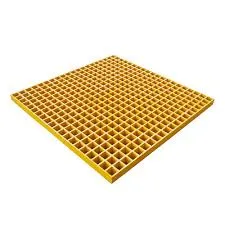
The term button tooth bit speaks to a design reliant on uniformly shaped carbide buttons distributed across the bit's face. These buttons are typically round and embed robustly into the bit, offering unparalleled durability and resistance to wear. This design is particularly beneficial in shattering hard rock formations, making it a preferred choice in extensive underground drilling and surface mining operations. Its durability extends the lifespan of the bit, reducing frequent replacements and, consequently, operational costs.
On the other hand, the toothed button bit adds a versatile edge to the drilling tool repertoire. Infusing its structure are teeth that enhance grip and penetration power, making it exceptionally capable of withstanding high-impact conditions. These bits excel in environments where precision and aggressive cutting are mandatory, such as oil and gas exploration and civil engineering projects. The teeth's acute angles help the bit maintain stability and reduce vibration, which often leads to improved accuracy and operational efficiency.
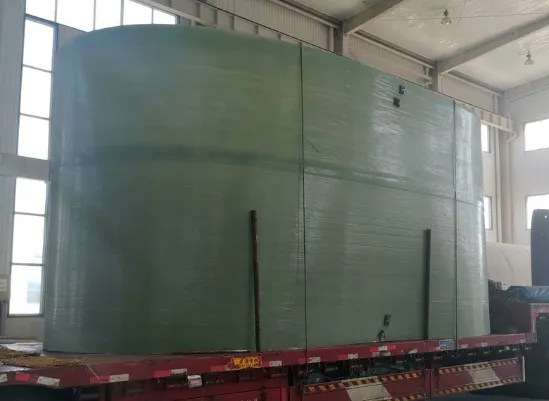
Embracing these tools involves weighing their respective benefits in accordance to specific project requirements. Should your operation require conquering particularly hard and abrasive surfaces, the button tooth bit’s ruggedness becomes indispensable. Its design ensures that the bit can endure challenging conditions without surrendering its effectiveness, thus maintaining the momentum of operational activities.
similar title to button tooth bit could be toothed button bit for ...
In contrast, scenarios demanding exactitude and deft handling of complex geological formations might find the toothed button bit to be of more value. Its engineered tooth-structure enhances its ability to engage with the strata, driving precise outcomes that flatter rigorous engineering blueprints. Additionally, this bit often affords faster penetration rates, improving project turnaround times — a critical factor in contracts tied to completion timelines and budgets.
Expert consultation heavily underscores the variance in selecting the appropriate bit based on geological survey data and intended drilling depth and width. Experienced drillers and engineers frequently rely on trial and error as well as advanced drilling simulations to determine which bit aligns optimally with the intended project's requirements, achieving greater control over the eventual outputs.
End users developing a preference between these bits must also weigh aspects like operational environment conditions, bit compatibility with pre-existing rigs, and long-term sustainability practices. Responsible utilization of button and toothed button bits contributes to reduced waste and improved project green ratings — aspects becoming increasingly critical in the global push toward more sustainable construction and exploitation practices.
Ultimately, investing in high-quality, well-suited drill bits such as the button tooth and toothed button bits can transform project dynamics. Their influence stretches beyond mere cost implications, touching on the reliable delivery of superior results time after time. As technology evolves, these bits continue to embody the cutting-edge advancements in material sciences and engineering, driving forward efficiencies that redefine industry standards.