Understanding the potential and advantages of FRP dual layer composite products is essential for industries seeking innovative solutions. These materials offer unprecedented durability, flexibility, and efficiency suitable for diverse applications. They represent a synthesis of advanced engineering and material science, driving the transformation of traditional manufacturing and construction methods.
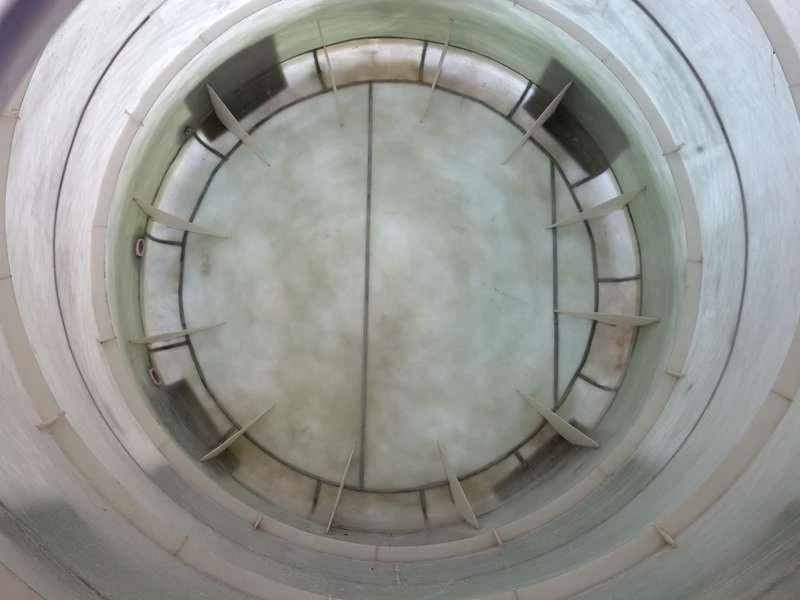
FRP, or Fiber Reinforced Polymer, dual layer composites are constructed using layers of reinforced fibers such as glass, carbon, or aramid (Kevlar) embedded within a polymer matrix. The dual layer design enhances their mechanical attributes, offering unique benefits over single layer composite or traditional materials like metals and concrete. This combination results in a product that benefits from the high strength-to-weight ratio, corrosion resistance, and thermal stability.
One of the defining experiences with FRP dual layer composites is their performance integrity under extreme environmental conditions. Industries such as aerospace, marine, and construction have begun to replace conventional materials with FRP composites due to their resilience. In regions where environmental conditions present severe challenges, such as coastal areas or regions with extreme temperature fluctuations, the robustness of FRP solutions becomes particularly advantageous. Their resistance to corrosion, stress, and chemical reactions significantly reduces maintenance costs and extends the service life of structures.
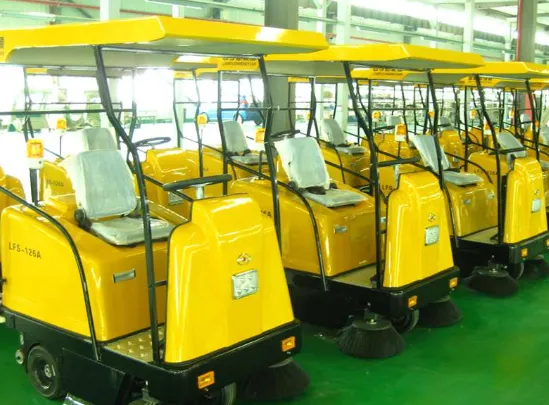
Expertise in the manufacturing process of FRP composites further highlights their superior quality. The process includes precise layering and curing techniques that ensure uniform strength and resilience across the product. These are crucial for industries demanding reliability and safety, such as bridge construction and aerospace. The innovative methods employed in creating these composites have made them indispensable in applications where safety is paramount, providing peace of mind and long-term sustainability.
frp dual layer composite product
Authority in the realm of FRP dual layer composites is validated through continuous research and technological advancements. Established manufacturers often collaborate with research institutions, leading to ongoing innovations that optimize the properties of these materials. This collaboration advances knowledge and assures clients that they are investing in products that stand on the cutting edge of material science. Many authoritative bodies have recognized FRP composites, endorsing their use in safety-critical applications due to their proven effectiveness.
The trustworthiness of FRP dual layer composites is rooted in both long-term performance data and the testimonials of satisfied customers across various sectors. A growing body of case studies outlines their successful implementation, demonstrating real-world achievements in load-bearing applications, seismic retrofitting, and beyond. Such case studies are vital in illustrating not just the theoretical potential of these materials, but their tangible benefits when put to the test in demanding environments.
Moreover, the lifecycle environmental impact of FRP composites significantly undercuts that of traditional materials. They contribute to environmentally sustainable practices due to their reduced weight, leading to lower transportation emissions, and the extended life cycle that limits the need for frequent replacements. Their role in sustainable development is increasingly becoming a cornerstone of their appeal.
In conclusion,
FRP dual layer composite products are at the fore of modern material innovation. They provide unparalleled advantages through enhanced durability, versatile applications, and sustainable credentials. For industries willing to embrace advanced composite technologies, these materials promise to open new realms of possibility, contributing to safer, cost-effective, and environmentally sustainable solutions. Investing in FRP dual layer composites not only meets the current industrial demands but prepares businesses for future challenges by leveraging the latest advancements in material science.