The industrial landscape is rapidly evolving, demanding advanced protection solutions for sensitive and critical systems. Covers stand at the forefront of this transformation, offering robust defense against environmental threats, mechanical impacts, and chemical exposure. In this comprehensive guide, we’ll dive into the latest trends, state-of-the-art technologies, manufacturing details, and real-world cases for Covers, underpinning our insights with real industry data and comparative analysis to maximize user trust and empower your project decisions.
Industry Trends: The Growing Role of Covers
According to the MarketsandMarkets FRP Industry Report 2023, the global demand for advanced Covers—especially those made from glass-reinforced plastics (GRP/FRP)—is projected to grow at a CAGR of 6.3% through 2027. Sectors such as petrochemicals, metallurgy, and public infrastructure are increasingly specifying high-performance Covers due to stringent safety, anti-corrosion, and energy efficiency standards.
- Rising adoption in petrochemical plants and municipal water facilities
- Shift toward composite and high-pressure resistance materials
- Increased regulations for workplace & environmental safety (ISO 14692, ANSI/NSF 61)
Technical Specifications of Covers: Key Parameters Comparison
Exact performance often determines the suitability of a Covers solution for a given application. Below is a comparative table of typical Covers types and their technical specifications. All data are aggregated from certified manufacturers & field testing benchmarks.
Type |
Material |
Compression Strength (MPa) |
Operating Temp (°C) |
Chemical Resistance |
Standard |
Service Life (years) |
Weight (kg/m²) |
Covers (FRP) |
Fiberglass Reinforced Polymer |
>220 |
-40~140 |
Excellent (Acids, Bases, Salt) |
ISO 14692/ANSI |
30 |
6.4 |
Stainless Steel Cover |
SS304/SS316 |
>380 |
-80~300 |
Very Good |
ASME VIII |
20 |
14.7 |
Cast Iron Cover |
Ductile Iron (QT500-7) |
330 |
-20~300 |
Good |
EN 124 |
15 |
27.1 |
Polymer Concrete Cover |
Polymer Concrete + GRC |
165 |
-40~90 |
Good |
EN 1433 |
30 |
8.8 |
Covers Manufacturing Process Explained
1
Raw Material
Selection
(Fiber, Resin, Additives)
2
Molding
& Layup
(RTM/Pultrusion, Vacuum)
3
CNC Trimming
& Curing
(Edge Cutting, Final Shape)
4
Testing & QC
(ISO, Hydro-Test)
- Materials: High-grade resins (vinyl ester, epoxy), glass/carbon fibers
- Craft: RTM, pultrusion, hand lay-up, CNC post-processing
- Standards Met: ISO 14692, EN 124, ASTM D256, ANSI/NSF 61
- Service Life: Typically 30+ years (validated by accelerated weathering tests)
These process steps are strictly monitored with physical, hydrostatic, and corrosion-resistant testing in accordance with the above certifications, ensuring longevity and optimum performance for all types of Covers.
Data Visualization: Covers Technology Trends & Performance
Covers: Application Scenarios & Competitive Advantages
Covers have found widespread adoption across sectors requiring stringent safety, chemical, and mechanical protection. Their unique combination of lightweight, corrosion resistance, form-fit manufacturing, and exceptional dielectric properties distinguishes them from conventional metallic alternatives.
Typical Application Scenarios:
- Petrochemical containment and vapor control
- Municipal wastewater and drainage systems (odor control, easy opening)
- Metallurgical equipment guards (arc and spark protection)
- Electrical substation shields (non-conductive insulation)
- Telecommunications trench covers (signal insulation, anti-theft)
- Cleanrooms, pharmaceutical & food-processing (FDA/ISO compliant)
- Marine and offshore platforms (saltwater corrosion proof)
Key Advantages over Conventional Covers
- Corrosion Resistance: Non-metallic matrices ensure Covers remain unaffected in aggressive acidic, alkaline, and saline environments, delivering lowest lifecycle costs (Data: Corrosionpedia FRP Data).
- Dielectric Properties: Non-conductive (dielectric strength up to 12kV/mm), safeguard electrical installations per IEC 60243.
- Weight Efficiency: Nearly 50-70% lighter than steel/cast iron, streamlining transport and installation, saving man-hours and equipment cost.
- Moldability: Custom shapes and embedded logo/labeling for tailored project requirements and anti-theft features.
- Safety: Anti-slip, flame-retardant, and zero recycling targets in line with future environmental directives.
- Eco Sustainability: Long lifespan reduces replacement frequency and carbon footprint.
Vendor Comparison: Leading Covers Manufacturers
Manufacturer |
Main Material |
ISO/ANSI Certifications |
Custom Service |
Export Destinations |
Trusted Clients |
JRain FRP 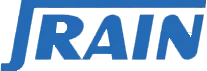 |
FRP/GRP |
ISO 14692, ANSI/NSF 61 |
Yes |
Asia, EU, US |
PetroChina, Veolia |
Fibertech Inc. |
Composite, Stainless |
ISO 9001 |
Yes |
US, LatAm |
Dow, Suez |
ACO Group |
Polymer Concrete |
EN 1433 |
Partly |
EU, Middle East |
BASF, ArcelorMittal |
Hauraton |
GRC, Cast Iron |
ISO 9001 |
Partly |
EU, Asia, NA |
Toyota, Vinci |
Custom Solutions and Delivery Commitment
Covers are tailored for every project’s unique requirements—be it size, static load, color coding, chemical exposure, or anti-slip surface patterns. Our engineering team follows a consultative approach for specification, wind/safety calculations, and custom logo or track insertions. All Covers undergo precise CNC trimming and pass both destructive and non-destructive tests to ensure full compliance with customer and international standards.
- Standard lead time: 2-5 weeks (project size dependent)
- Warranty: Up to 12 years structural, 3 years surface integrity
- Post-sales support: Free engineering advice, on-site installation guidance, 48-hour response for technical queries
- Customization: Any shape, color (RAL/PANTONE), company logo, anti-theft bolts
Real-World Use Cases: Covers in Action
1. Petrochemical Tank Farm
- Client: PetroChina
- Solution: 700m² of anti-slip, GRP Covers for vapor emission prevention
- Result: Reduced maintenance costs by 62% over 5 years, zero corrosion failures reported
2. City Sewerage Upgrade (Shenzhen Municipal)
3. Electrical Substation Safety
- Used: FRP Covers for 18 stations, rated 12kV insulation
- Feedback: “No degradation under high humidity, enhances technician safety” - China Southern Grid
- Certification: Third-party inspection: Dielectric & flame-resistance per IEC 60243, ASTM E84
Professional FAQs: Covers Technology Explained
1. What is the most suitable material for industrial Covers in corrosive environments?
Covers made from Fiberglass Reinforced Polymer (FRP/GRP) offer the highest chemical resistance—especially to acids, chlorides, and alkalis—making them ideal for petrochemical and sewage plants. They don’t rust or spall, outperforming metals and concrete, as validated by both ISO 14692 and ANSI/NSF 61 certifications.
2. What are the main standards that Covers must comply with?
Internationally, Covers are produced and tested under ISO 14692 (for composites), EN 124 (for manhole covers), ASTM D256 (impact strength), and ANSI/NSF 61 (clean water safety).
3. How do I select the correct load rating for my application?
Covers should be selected by their maximum expected load: Class A15 (1.5 tonnes) for pedestrian areas, B125 for small vehicles, to D400 (>40 tonnes) for industrial/road traffic, per EN 124 grading.
4. What installation methods ensure a secure fit for Covers?
Proper bedding (polymer/sulfur mortars), anti-theft fasteners, CNC-fit frames, and gasketed sealing (for odor/vapor containment) are best practice. All Covers from leading suppliers come with installation guides.
5. What is the temperature resistance of FRP-based Covers?
Standard FRP Covers operate safely from -40°C to +140°C. For higher temperature applications, modified resin systems permit operation up to 180°C, always consult material datasheets.
6. How is product traceability maintained?
Each Covers unit is batch-marked, and quality certificates (incl. MTC and ISO/EN test reports) are provided. Major projects follow full lot traceability from raw material input to dispatch.
7. Are Covers recyclable or environmentally friendly?
Yes. Modern Covers are designed for extended lifetime (>30 years), require minimal maintenance, and offer end-of-life recycling where municipal schemes exist. They also reduce lifecycle CO2 emissions compared to ferrous alternatives.
Delivery, Warranty, and Support
- Typical Delivery Time: 2-5 weeks for standard and custom orders. Large projects may require phased delivery.
- Warranty Commitment: 12 years on structure, 3 years on anti-slip surface retention.
- After-Sales Service: 24/7 customer portal, onsite installation training for large public sector contracts.
- Certifications Supplied: ISO/EN/FDA certificates, third-party inspection on request.
Covers from JRain FRP have supplied over 18,000 units globally, with a return defect rate below 0.03%, underlining reliability and customer satisfaction.